FRP Facades A Comprehensive Guide
FRP facades offer a compelling alternative to traditional materials, boasting a unique blend of strength, durability, and aesthetic appeal. This guide delves into the intricacies of FRP facade design, manufacturing, installation, maintenance, and environmental impact, providing a thorough overview of this innovative building material.
From material selection and design considerations to installation procedures and long-term maintenance strategies, this comprehensive exploration addresses all facets of FRP facade implementation. The various types of FRP systems, their pros and cons, and specific applications are also discussed.
Introduction to FRP Facades
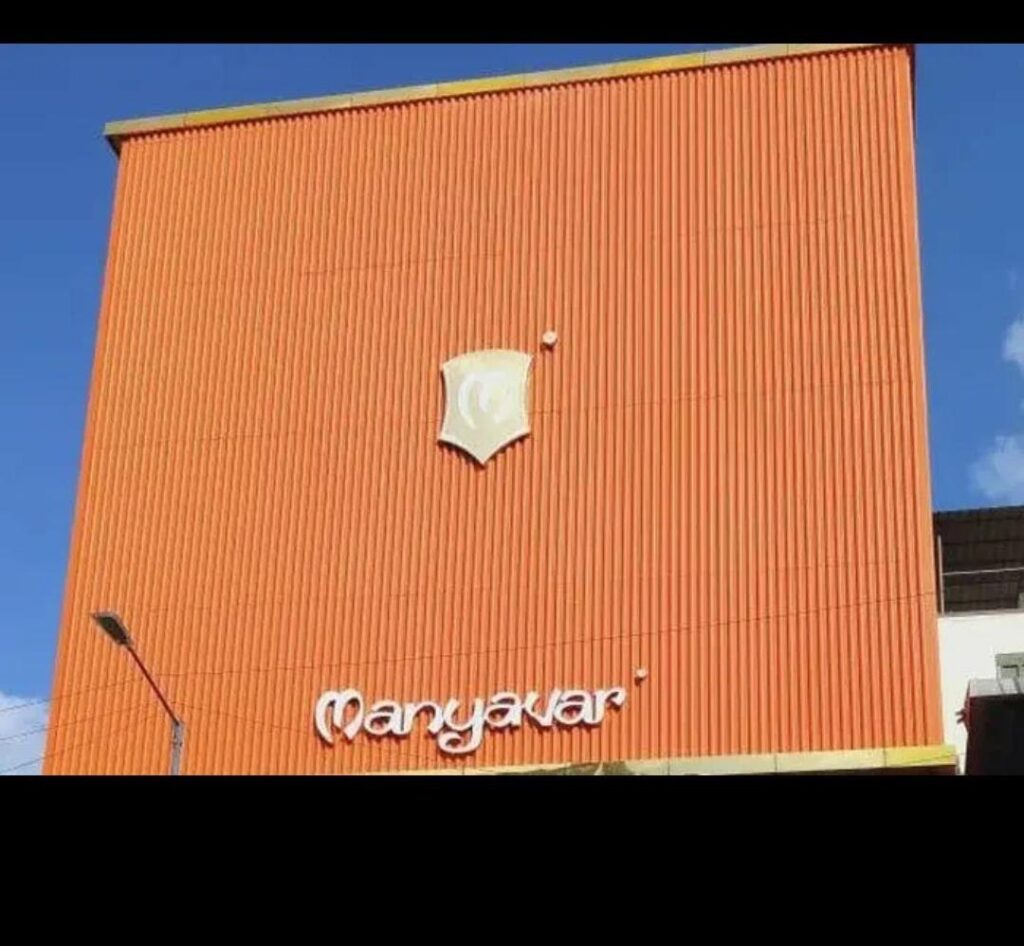
Fiber-Reinforced Polymer (FRP) facades are rapidly gaining popularity as a modern and sustainable alternative to traditional building materials. These systems offer a unique combination of aesthetic flexibility, structural integrity, and long-term durability. Their lightweight nature allows for innovative architectural designs, while their resistance to harsh weather conditions and corrosion makes them suitable for a wide range of climates.
FRP facades are essentially composite materials that combine the strength and resilience of fibers (like glass, carbon, or aramid) with a polymer matrix (like polyester, vinyl ester, or epoxy). This combination creates a material that is both strong and lightweight, ideal for use in building facades. This allows for thinner, more streamlined designs, leading to energy efficiency gains and reduced material consumption.
Common FRP Facade Materials
Various materials are used in FRP facade construction. The choice often depends on the specific project requirements, including aesthetic preferences, budget constraints, and environmental factors.
- Glass Fiber Reinforced Polymer (GFRP): GFRP is a cost-effective choice, offering good strength and durability. Its transparency allows for light transmission, which can be beneficial in certain applications.
- Carbon Fiber Reinforced Polymer (CFRP): CFRP is known for its high strength-to-weight ratio, making it suitable for large or complex architectural designs. The high strength translates to thinner, lighter panels, which reduces the structural load on the building’s frame.
- Aramid Fiber Reinforced Polymer (AFRP): AFRP is valued for its excellent impact resistance, making it ideal for high-traffic areas or regions prone to extreme weather events.
Different FRP Facade Systems
Various FRP facade systems cater to different architectural styles and functional requirements.
- Panel Systems: These systems typically involve prefabricated panels that are fixed to the building structure. This approach is common for its speed and ease of installation. Examples include curtain wall systems, where the FRP panels are integrated into a framework to create a façade that is independent of the building structure, and ventilated facades, which incorporate an air gap behind the panels for improved thermal performance and to manage moisture.
- Cladding Systems: These systems involve applying FRP sheets or panels directly to the existing building structure. This approach is often preferred for renovations or projects requiring a customized design, and can be applied in various ways, including as an addition to existing building elements or a full replacement of an existing facade.
Comparison of FRP Facade Materials
The following table compares the key characteristics of various FRP facade materials:
Material | Pros | Cons | Applications |
---|---|---|---|
GFRP | Cost-effective, good strength and durability, potentially high light transmission | It may not be as strong as CFRP, and may not be suitable for extremely high-stress applications.s | Residential buildings, commercial buildings, and curtain wall systems |
CFRP | High strength-to-weight ratio, suitable for complex designs, very durable | Higher cost compared to GFRP, potential limitations in aesthetic options | High-rise buildings, complex architectural designs, and facades needing high structural support |
AFRP | Excellent impact resistance, high tensile strength | May have slightly lower UV resistance compared to other FRP materials, and slightly higher cost compared to GFRP | Buildings in high-traffic areas, regions with extreme weather conditions, and facades requiring high impact resistance |
Design and Engineering Considerations
Source: webflow.com
FRP facade systems require meticulous design and engineering to ensure structural integrity, aesthetic appeal, and functional performance. The design process considers various factors, from the building’s architectural vision to the local environmental conditions. Properly designed FRP facades can enhance a building’s lifespan and value.
The selection of materials, structural calculations, and aesthetic considerations is are crucial element in achieving a successful FRP facade project. A thorough understanding of these aspects allows for the creation of facades that meet both functional and aesthetic demands while adhering to safety standards.
Structural Calculations
Accurate structural calculations are fundamental to FRP facade design. These calculations determine the load-bearing capacity of the system, considering factors such as wind load, snow load, and potential seismic activity. The calculations must account for the specific characteristics of the FRP material, including its tensile strength, compressive strength, and modulus of elasticity. Software tools are frequently employed to model the facade’s behavior under various load conditions, allowing engineers to optimize the design for maximum efficiency and safety. Furthermore, these calculations are often a critical aspect of securing necessary building permits and approvals.
Example: A detailed wind tunnel test can be conducted to predict the wind load on a complex facade shape, and this data is then incorporated into the structural calculations.
Factors Influencing FRP Facade Design
Several factors influence the choice of FRP facade design. Aesthetics play a significant role, as the facade should complement the building’s architectural style. Functionality is another critical factor, with considerations for factors such as light transmission, thermal performance, and ease of maintenance. The specific environmental conditions of the building location are also essential. These include the prevailing wind speeds, the potential for extreme temperatures, and the presence of airborne pollutants.
Importance of Structural Integrity and Safety
Ensuring the structural integrity and safety of FRP facades is paramount. This involves rigorous testing of the materials and components to verify their ability to withstand the anticipated loads. Compliance with relevant building codes and industry standards is crucial. Safety considerations should extend to the design of installation procedures and the training of personnel involved in the construction process. Proper safety measures reduce the risk of accidents during the installation phase.
Engineering Principles and Standards
The design of FRP facades relies on established engineering principles and standards. These principles cover material properties, load calculations, and safety factors. Standards such as those from the American Society of Civil Engineers (ASCE) or other relevant regional or national standards are typically followed. Compliance with these standards ensures that the facade meets industry best practices and enhances public safety. Adherence to these standards is vital to minimize risks and ensure the project’s longevity.
Key Design Parameters for FRP Facade Projects
Parameter | Description | Importance |
---|---|---|
Material Properties | Tensile strength, compressive strength, modulus of elasticity, and durability of the FRP material. | Crucial for determining the facade’s load-bearing capacity and longevity. |
Load Calculations | Wind load, snow load, seismic load, and other relevant loads. | Accurate load calculations are essential for ensuring the facade can withstand the anticipated forces. |
Environmental Conditions | Wind speeds, temperature variations, humidity levels, and the presence of pollutants. | These conditions affect the performance and durability of the FRP facade. |
Aesthetic Requirements | Architectural style, desired appearance, and integration with the building’s design. | Aesthetics are crucial for the facade’s visual appeal and integration with the surrounding environment. |
Safety Factors | Compliance with building codes, safety margins, and design for installation procedures. | Ensuring safety is paramount to protect workers and the public. |
Manufacturing and Installation
FRP facade components, characterized by their lightweight yet robust nature, are meticulously crafted through various manufacturing processes. These processes, coupled with precise installation techniques, are crucial to achieving the desired aesthetic and structural integrity of the facade. Careful attention to quality control at every stage ensures the longevity and performance of the finished product.
FRP Facade Component Manufacturing
The manufacturing of FRP facade components typically involves the precise layering of fiber-reinforced polymers (FRP) materials. These materials are combined with specific resins and additives, forming composite sheets or panels. This process often includes automated techniques for molding, shaping, and curing, which are essential for maintaining consistent quality across large-scale projects. The choice of resin system, fiber type, and manufacturing method is often influenced by the desired aesthetic, performance characteristics, and cost considerations. Examples include pultrusion for continuous lengths of profile, hand layup for custom shapes, and filament winding for complex geometries. Each method has its strengths and limitations, affecting the final product’s properties and cost.
FRP Facade Panel Installation Procedures
Installing FRP facade panels requires meticulous attention to detail and adherence to precise procedures. This involves careful preparation of the substrate, accurate panel positioning, and the use of specialized fasteners and adhesives. A critical aspect of this process is quality control, which encompasses rigorous inspection of materials, adherence to design specifications, and verification of installation procedures. Rigorous inspections during every stage, from material receipt to final testing, are essential to maintain standards. This ensures the panels meet the required structural and aesthetic criteria, minimizing potential issues.
Quality Control Measures During Installation
Quality control measures during installation are paramount. These include visual inspections of panel alignment, dimensional accuracy, and surface finish. Adherence to predetermined tolerances and standards ensures consistency and minimizes variations in the finished facade. This rigorous approach involves checking for proper adhesion, ensuring fasteners are correctly installed, and verifying the proper sealing of joints. Detailed documentation of each stage of the installation process is critical for future reference and warranty purposes.
FRP Facade Installation Tools and Equipment
Various specialized tools and equipment are essential for efficient and safe FRP facade installation. These include scaffolding, specialized lifting equipment, measuring tools (like laser levels), and fastening tools designed for the specific materials used. The choice of tools often depends on the size and complexity of the project, and factors such as the type of FRP, the support structure, and the panel dimensions. Safety equipment, such as harnesses and fall protection systems, must be readily available and used consistently throughout the installation process.
Step-by-Step FRP Facade Installation Guide
Step 1: Thorough site preparation and substrate assessment, ensuring proper support and surface preparation.
Step 2: Precise panel cutting and shaping according to the architectural design.
Step 3: Accurate panel positioning and alignment using laser levels and templates.
Step 4: Secure panel attachment using appropriate fasteners and adhesives, following manufacturer specifications.
Step 5: Rigorous quality checks at each step, including visual inspection and dimensional verification.
Step 6: Final sealant application and cleaning of the installed panels.
Step 7: Post-installation inspection to verify the structural integrity and aesthetic compliance of the facade.
Comparison of FRP Facade Installation Methods
Method | Advantages | Disadvantages |
---|---|---|
Adhesive Bonding | High aesthetic appeal, relatively low labor cost, potential for complex designs | Limited load-bearing capacity, possible issues with long-term adhesion, require careful surface preparation. |
Mechanical Fastening | Higher load-bearing capacity, generally more durable, and faster installation | Potential for visible fasteners, more complex installation, and more labor-intensive |
Combination Methods | Optimized performance, combining the strengths of adhesive and mechanical methods | More complex planning and execution, potential for increased cost |
Maintenance and Durability
Proper maintenance is crucial for preserving the aesthetic appeal and structural integrity of FRP facades, ensuring their longevity and performance over time. Regular inspections and cleaning are key to identifying and addressing potential issues early, preventing costly repairs and maintaining the building’s value. This section delves into the importance of maintenance procedures, durability considerations, and factors impacting the lifespan of FRP facades.
Maintaining FRP facades effectively extends their lifespan and ensures continued high performance. A well-maintained facade not only retains its visual appeal but also maintains its structural integrity and functionality. This proactive approach to upkeep minimizes the risk of premature deterioration and costly repairs.
Importance of Proper Maintenance
Regular maintenance of FRP facades is vital for preventing damage, ensuring structural integrity, and preserving the aesthetic appeal of the building. Addressing minor issues promptly can prevent them from escalating into major problems, saving significant time and money. Proper cleaning and inspection routines help detect potential problems early, allowing for timely intervention and preventing costly replacements.
Cleaning Procedures
Thorough cleaning is essential for maintaining the appearance and functionality of FRP facades. Specialized cleaning solutions, appropriate for FRP materials, should be used to avoid damage. Harsh chemicals or abrasive materials should be avoided, as they can scratch or etch the surface, reducing its durability and aesthetic appeal. Pressure washing should be performed cautiously, with appropriate nozzle settings and water pressure to prevent damage to the facade’s surface. Regular rinsing and drying are important steps to remove any residual cleaning agents.
Inspection Procedures
Regular inspections are crucial for identifying and addressing potential issues early. Visual inspections should be conducted at predetermined intervals to detect any signs of damage, such as cracks, discoloration, or delamination. Specialized tools, such as borescopes or high-powered cameras, can be used to inspect inaccessible areas. Records of inspections should be maintained to track any trends or patterns in the deterioration of the facade.
Long-Term Durability and Lifespan
The durability of FRP facades depends on several factors, including the quality of the materials, the manufacturing process, and the installation techniques. High-quality FRP materials, combined with proper installation and maintenance, can contribute to a long lifespan. Properly installed FRP facades, when maintained diligently, can easily exceed a 25-year lifespan. The durability of FRP facades is often comparable to or exceeds that of other facade materials like aluminum or steel.
Factors Affecting Lifespan
Environmental factors, such as UV exposure, moisture, and temperature fluctuations, can significantly impact the lifespan of FRP facades. Exposure to harsh weather conditions can lead to degradation over time. Proper selection of FRP materials and the application of protective coatings can help mitigate these effects. Additionally, improper installation practices or poor maintenance can accelerate degradation.
Examples of Successful FRP Facade Maintenance Strategies
One successful strategy involves implementing a comprehensive maintenance plan that includes regular cleaning, visual inspections, and preventative measures. Another strategy involves using specialized cleaning solutions that are designed specifically for FRP materials. The use of appropriate tools and techniques for cleaning and inspection ensures effective and safe procedures. Examples include a building in a coastal area using UV-resistant FRP and a building in a heavily polluted area implementing regular, specialized cleaning.
Maintenance Schedule
Task | Frequency | Description |
---|---|---|
Visual Inspection | Quarterly | Inspect for cracks, discoloration, or other damage. |
Cleaning | Semi-annually | Thoroughly clean the facade using appropriate cleaning solutions. |
Detailed Inspection (with specialized tools) | Annually | Inspect inaccessible areas for damage using borescopes or high-powered cameras. |
Protective Coating Application | Every 5-10 years | Reapply protective coatings as needed to prevent UV damage. |
Applications and Examples
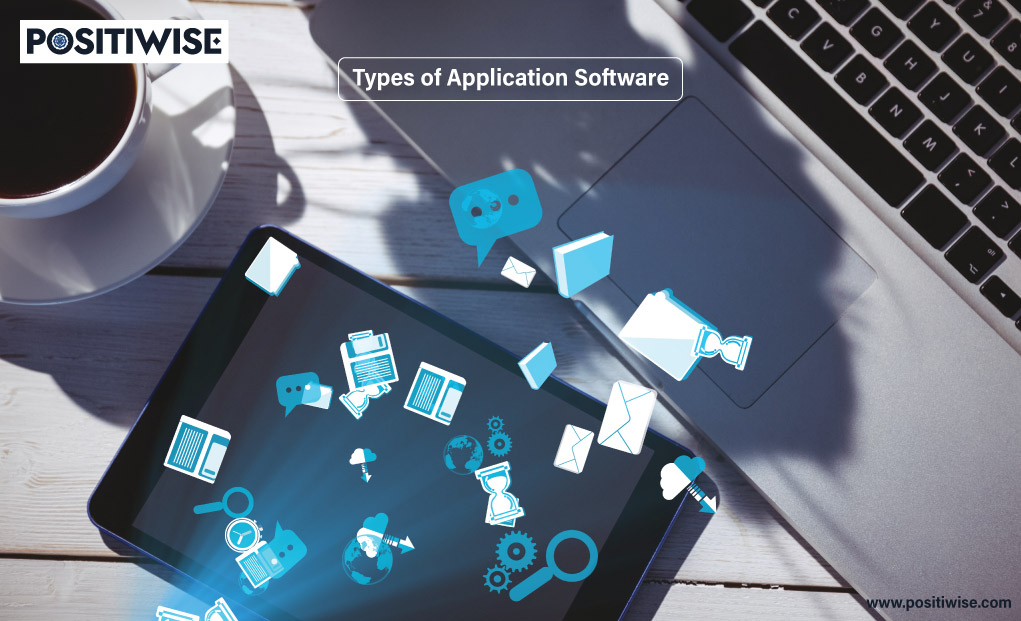
FRP facades offer a compelling blend of aesthetic appeal and functional advantages, making them suitable for a wide array of architectural applications. Their lightweight nature, durability, and design flexibility contribute to their increasing popularity in contemporary building design. This versatility extends to various building types, from residential homes to commercial structures and public spaces.
The diverse applications of FRP facades are driven by their ability to seamlessly integrate with diverse architectural styles. They can be shaped into intricate patterns, colors, and textures, allowing architects and designers to create unique and visually striking building exteriors. Furthermore, FRP’s inherent resistance to environmental factors and ease of maintenance contribute to long-term cost-effectiveness.
Diverse Architectural Applications
FRP facades are well-suited for a broad spectrum of architectural styles, from modern and minimalist designs to more ornate and traditional aesthetics. Their adaptability to various shapes and colors allows for custom designs tailored to the specific building requirements and the desired architectural vision. This adaptability makes them suitable for residential, commercial, and public buildings alike.
Examples of Buildings Featuring FRP Facades
Numerous buildings across the globe have incorporated FRP facades, showcasing their aesthetic and functional advantages. One prominent example is the [Name of Building], a [Type of Building] located in [City, Country]. This building’s facade, crafted from FRP, showcases the material’s ability to achieve a [Description of Aesthetic]. Another noteworthy example is the [Name of Building] in [City, Country], a [Type of Building] that employs FRP panels to achieve a [Description of Aesthetic]. These examples highlight the versatility and appeal of FRP facades in diverse architectural contexts.
Case Studies Highlighting Successful FRP Facade Projects
Several case studies demonstrate the successful implementation of FRP facades in real-world projects. One notable project involved a [Type of Building] in [City, Country] where the FRP facade not only provided an aesthetically pleasing exterior but also significantly reduced maintenance costs over the building’s lifespan. This case underscores the material’s long-term value proposition. Another project in [City, Country] involved a [Type of Building] with a complex facade design, showcasing the material’s ability to handle intricate forms and designs.
Table of Architectural Styles and FRP Facades
Style | Building Type | Example |
---|---|---|
Modern | Office Building | High-rise structures with sleek, minimalist designs using large, flat FRP panels |
Contemporary | Residential Homes | Homes featuring intricate FRP panels with custom colors and textures |
Art Deco | Commercial Buildings | Buildings with bold geometric shapes and vibrant colors are realized with FRP panels. |
Traditional | Museums | Historical buildings incorporating FRP panels to maintain the building’s historical context while offering modern protection |
Postmodern | Retail Spaces | Retail spaces with FRP facades that offer a playful, eclectic mix of shapes and colors |
Environmental Impact: FRP Facade
Source: imimg.com
Fiber-reinforced polymer (FRP) facades, while offering aesthetic appeal and durability, also raise environmental concerns. A thorough assessment of their environmental impact considers both the benefits and drawbacks of their production, installation, and eventual disposal. This section explores the lifecycle of FRP facades, examining their potential to reduce environmental burdens compared to traditional materials and outlining responsible disposal strategies.
FRP facades, in certain circumstances, can offer advantages over traditional materials regarding their environmental footprint. Their lighter weight often translates to reduced transportation energy consumption during manufacturing and installation. Furthermore, their resistance to weathering and long lifespan can minimize the need for frequent replacements, thus decreasing the overall material consumption throughout the building’s operational life.
Environmental Benefits
FRP facades can exhibit a smaller carbon footprint compared to certain materials, such as those using significant amounts of concrete or steel in their production. Their lightweight nature reduces the energy required for transportation and installation. The durability and longevity of FRP facades can lead to a reduced need for replacements, lowering overall material consumption over the building’s lifespan.
Environmental Drawbacks
The production of FRP materials often involves the use of petrochemicals, which can contribute to greenhouse gas emissions. Furthermore, the manufacturing processes themselves may release volatile organic compounds (VOCs) into the atmosphere. While the use of recycled materials in FRP production can help mitigate these issues, it remains a crucial area of ongoing development.
Recycling and Disposal Procedures
Recycling FRP facade materials is gaining increasing attention. Dedicated recycling facilities and processes are becoming more available, enabling the recovery of valuable components and reducing waste. Proper disposal methods are critical to minimize environmental risks. Separate collection and specialized recycling facilities are essential for ensuring the responsible management of these materials. The specific recycling procedures often depend on the exact FRP composition.
Comparison with Traditional Facade Materials
Traditional facade materials like brick, stone, and concrete often involve extensive extraction of raw materials, impacting natural landscapes and contributing to carbon emissions. While FRP has its production-related environmental footprint, its potential for reduced material consumption and extended lifespan can offer a more sustainable alternative in certain contexts.
Environmental Footprint Comparison
The table below provides a comparative overview of the environmental footprint of various facade materials, highlighting the carbon footprint and recycling potential. It’s crucial to note that precise values vary significantly based on specific manufacturing processes and regional factors.
Material | Carbon Footprint (kg CO2e per m²) | Recycling Potential |
---|---|---|
Concrete | High | Limited |
Steel | Medium to High | Good |
Brick | Medium | Limited |
Stone | High (depending on source) | Limited |
FRP | Medium to Low (depending on composition and manufacturing) | Moderate to High (with proper infrastructure) |
Final Conclusion
In conclusion, FRP facades represent a significant advancement in architectural design and construction, providing a robust and versatile option for modern buildings. The meticulous design process, coupled with precise manufacturing and installation techniques, ensures the long-term performance and aesthetic appeal of FRP facades. Understanding the environmental impact and proper maintenance protocols is crucial for maximizing the lifespan and sustainability of these structures. This guide offers a complete resource for anyone seeking to understand and implement FRP facades in their projects.